PROJEKTE
Koordinator des Verbundvorhabens:
Prof. Dr.-Ing. Sebastian Härtel
Förderkennzeichen: 03WIR2510
Laufzeit: 01.11.2023 – 31.10.2025
Das Bündnis „Digitale Reparaturfabrik“ – Digitalisierung der Wartung, Instandhaltung und Reparatur hat sich in der ersten Förderperiode als Ziel gesetzt, auf Grundlage des Innovationsfeldes der Wartung, Instandhaltung und Reparatur zentrale Akteure der Region zukunftsfähig zu vernetzen. Ihr Ziel ist die Etablierung einer Circular Economy auf Bauteilebene, die durch die Entwicklung und Vertiefung von Innovationsfeldern wie KI-basierter Analytik, zirkulärer Instandhaltungs- und Reparaturverfahren, sowie digitalem Datenmanagement vorangetrieben wird. Eines der Projekte innerhalb dieses Bündnisses, die „Inline-Prozesskettenentwicklung für Reparaturverfahren zum Recycling von AMC-Werkstoffen“,realisiert diese Ziele durch die Kombination von additiver und umformtechnischer Fertigung.
Die angestrebte ressourceneffiziente (Inline)-Prozesskette zielt darauf ab, die Eigenschaften der AMC Leichtbauwerkstoffe bei der additiven Verarbeitung gezielt einzustellen und gleichzeitig Fehlstellen kompensieren. Dies wird durch eine Kombination aus innovativen Prozessen, wie der inkrementellen Umformung und Wärmebehandlung, erreicht. Das Vorhaben verfolgt verschiedene Ziele, darunter die Umsetzung einer Recycling-Strategie, die Weiterentwicklung von AMC-Werkstoffen und die Integration von Bearbeitungsköpfen zur Nachbehandlung in einem Industrieprozess.
Das Projekt trägt zur Strukturstärkung der Regionen in Ostdeutschland bei und strebt eine enge Zusammenarbeit zwischen Wissenschaft und Wirtschaft an. Es betont die Bedeutung von Innovationen, insbesondere im Bereich der AMC-Werkstoffe, und stellt die Entwicklung einer gemeinsamen Herstellungsstrategie in den Mittelpunkt. Das Vorhaben zeigt die Einzigartigkeit der mobilen Reparaturfabrik, die durch dieses Projekt weiter differenziert wird. Es adressiert aktuelle Marktlücken in Bezug auf die mobile Reparatur von Bauteilen mit AMC-Werkstoffen und hebt die Potenziale des WAAM-Prozesses und AMC-Werkstoffe in verschiedenen Industriebereichen auf eine neue Ebene.
Beteiligte Partner:
ACCESS e.V.
METROM Mechatroninische Maschinen GmbH
BTU Fachgebiet Elektronische Schaltungstechnik
Mobile Reparaturfabrik
Koordinator des Verbundvorhabens:
Prof. Dr.-Ing. Sebastian Härtel
Förderkennzeichen: 03WIR2503
Laufzeit: 01.03.2021 – 31.10.2023
In diesem Teilprojekt möchten mehrere Akteure aus der Region gemeinsam eine einzigartige Technologieplattform für die mobile Reparatur entwickeln. Hierdurch soll eine nachhaltige regionale Allianz im Bereich der schweißtechnischen Reparaturverfahren gebildet werden, die die mobile Reparaturplattform als technologische Basis für gemeinsame Innovationen nutzen möchte.
Die Plattform kombiniert die spanende Bearbeitung mit drei Auftragschweißlösungen für die Reparatur mit fortschrittlichen Sensorsystemen und kann somit gesamte Prozessketten in einer mobilen Lösung abdecken. Sie ist außerdem als einzige Lösung am Markt modular mit Lichtbogen-, Plasma- und Laserquellen bestückbar. Diese Vielseitigkeit wird durch die branchenspezifischen digitalen Assistenzsysteme ausgebaut, die mit den jeweiligen Partnern entwickelt werden.
Beteiligte Partner:
ACCESS e.V.
B.I.G.
BTU Cottbus-Senftenberg
GEFERTEC
Kjellberg Finsterwalde
OSCAR PLT
Scansonic
Assoziierte Partner:
LEAG
Rolls-Royce Deutschland Ltd & Co KG
SIK Peitz GmbH
Mobile Fablabs: WI+R Verbundwerkstatt Lausitz
Koordination des Verbundvorhabens:
LSWI – Universität Potsdam
Förderkennzeichen: 03WIR2506
Laufzeit: 01.06.2021 – 31.05.2023
Das Verbundvorhaben „Mobilefablabs: WI+R Verbundswerkstatt Lausitz“ (MoFab) erforscht offen gestaltete Innovationsprozesse im Kontext von Wartung, Instandhaltung und Reparatur, die auf die Beteiligung der Lausitzer Bürgerschaft ausgerichtet sind. Fokussiert werden die lausitzspezifischen Themengebiete Mobilität, Wassernutzung, Industrie und Kultur. Das Vorhaben ist darauf ausgerichtet, Dynamiken zwischen lokalen Problemstellungen und modernen Technologien herzustellen, die im weiteren Verlauf zu Demonstratoren entwickelt werden. Im Ergebnis steht ein soziales Innovationmodell sowie konkrete Lösungen aus der Bürgerschaft.
Teil des Konsortiums sind der Open Knowledge Foundation Deutschland e.V., der AWO Brandenburg Süd e.V., der Wissenschaftsladen Potsdam e.V. und die Universität Potsdam, mit dem Lehrstuhl für Wirtschaftsinformatik, insb. Prozesse und Systeme.
Mobiles IR-Thermografieverfahren
Koordinator des Verbundvorhabens:
Dipl.-Ing. Dustin Nielow
Förderkennzeichen: 03WIR2504
Laufzeit: 01.12.2020 – 31.11.2022
Faserkunststoffverbunde (FKV) werden in der Lausitz in Großbauteilen der Windenergie und im Schienenfahrzeugbau eingesetzt. Beide Branchen benötigen automatisierte, kostengünstige Verfahren zur Schadensdetektion und Ableitung von Reparatur-Konzepten, welche die gängige subjektive Analyse durch visuelle Begutachtung und Klopfprüfung ersetzen können. Infrarot-Thermografie ist hierfür prädestiniert, da eine berührungslose Analyse aus der Entfernung mit einem großen Bildfeld möglich ist.
In enger Kooperation mit den Projektpartnern BTU Cottbus-Senftenberg (Fachgebiete Polymerbasierter Leichtbau (PBL) und Elektronische Schaltungstechnik (ES)), der Berliner Nanotest und Design GmbH, dem Fraunhofer-Institut für Angewandte Polymerforschung IAP mit dem Forschungsbereich Polymermaterialien und Composite PYCO sowie assoziierten Projektpartnern der regionalen Windenergie (Wartung und Reparatur) werden in diesem Vorhaben die Grundlagen für den Außeneinsatz der IR-Thermografie an FKV-Großbauteilen erarbeitet und ein entsprechender Prototyp für die IR-Prüfung entwickelt.
Das Fachgebiet Elektronische Schaltungstechnik unter Professor Schacht und die Nanotest und Design GmbH bringen Kompetenzen in der Thermografie mikroelektronischer Baugruppen für die Entwicklung einer entsprechenden IR-Prüfmethodik, bestehend aus Prüfgerät und Auswerteanalyse ein. Das PYCO und das Fachgebiet Polymerbasierter Leichtbau unter Professor Seidlitz bringen die nötigen Kompetenzen in FKV-Herstellungstechnologien für die Fertigung repräsentativer Prüfkörper sowie deren reproduzierbare und realistische Schädigung mittels eines instrumentierten Fallgewichtsturms ein. Der Einsatz von zerstörungsfreier (μCT und Ultraschall) und zerstörender (Schliffbilder) Werkstoff- und Bauteilprüfung dient der Analyse der eingebrachten Schäden und der Validierung der neuentwickelten IR-Prüfmethodik.
Digitalisierung in der Materialprüfung
Koordinator des Verbundvorhabens:
Prof. Dr.-Ing. Matthias Ziegenhorn
Förderkennzeichen: 03WIR2505
Laufzeit: 01.04.2021 – 31.03.2024
Die im Teilprojekt angestrebte Lösung zielt erstmalig darauf ab, digital vernetzte Prozessabläufe für die Materialprüfung bei der Anwendung von digitalen Fertigungsverfahren für die Reparatur von Bauteilen in Maschinen und Anlagen zu schaffen, die eine Garantie auf die Bauteileigenschaften beinhalten. Dabei müssen verschiedene Wissensgebiete interdisziplinär zusammengeführt und eine regionale Allianz zwischen Forschungsstellen, Prüflaboren und Endanwendern gebildet werden.
Die Teilprojektidee des Partners BTU besteht im experimentellen Erforschen von Zusammenhängen zwischen den Prozessparametern beim digitalen Fertigungsprozess und den resultierenden Festigkeitseigenschaften für einen prototypischen Fall. Durch Auswahl und Anpassung von festkörpermechanischen Modellen wird in der Folge das Beanspruchungsverhalten der Bauteile beschrieben und prognostiziert letztlich auf weitere Fälle verallgemeinert.
Beteiligte Partner:
BTU Cottbus-Senftenberg
Grasse Zur Ingenieurgesellschaft mbH, Berlin
imq – Ingenieurbetrieb GmbH, Hagenwerder
TAKRAF GmbH, Lauchhammer
Vattenfall Hydro GmbH, Berlin
Assoziierte Partner:
Lausitz Energie Bergbau AG, Cottbus
Additive Ersatzteilfertigung
Koordinator des Verbundvorhabens:
Prof. Dr.-Ing. Sebastian Härtel
Förderkennzeichen: 03WIR2507
Laufzeit: 01.04.2021 – 30.09.2023
Zahlreiche Unternehmen in der Lausitz sind im metallverarbeitenden Gewerbe tätig. Der zunehmende Wegfall der Primärindustrie in den kommenden Jahren stellt diese Unternehmen vor die Herausforderung des eigenen Wandels. Als eine der zukunftsweisendsten Entwicklungen in der Metallverarbeitung gilt die additive Fertigung. Entwicklungen der letzten Jahre und aktuelle Prognosen zeigen, dass Additive Manufacturing (AM) weiter an Bedeutung gewinnen und in immer mehr Einsatzbereichen Durchbrüche erzielen wird.
An der BTU wurden in den letzten Jahren umfangreiche Kompetenzen im Bereich der additiven Fertigung aufgebaut. So wurden in den letzten fünf Jahren ca. 5 Mio. Euro an Ausstattung und zahlreiche Förderprojekte eingeworben. Aufgrund der positiven Entwicklungen hat sich die Brandenburgische Landesregierung im März 2019 entschlossen, den Aufbau eines 3DLABs an der BTU mit 12,5 Mio. € zu fördern. Mit dem 3DLAB wird die Infrastruktur bereitgestellt, um die gesamte Prozesskette der additiven Fertigung von der Herstellung des Ausgangswerkstoffs (Pulver und Draht) bis hin zum fertig bearbeiteten und geprüften Bauteil abzubilden. Diese positiven Impulse haben dazu beigetragen, dass sich im WIR!-Bündnis WI+R ein regionales Netzwerk aus unterschiedlichen Branchen (Maschinenbau, Fertigung, Luftfahrt, Schienenverkehr, Energietechnik, Materialdatenbanken/Software) bilden konnte. In der Konzeptphase der WIR!-Initiative wurde das Innovationsfeld der additiven Ersatzteilherstellung identifiziert, das den Kern des vorliegenden Teilprojekts bildet. Die im Projekt beteiligten Endanwender Rolls-Royce, Deutsche Bahn AG und LEAG prognostizieren bereits heute, dass durch den Wegfall von Lieferanten (z.B. durch Insolvenz, Umstrukturierung) zahlreiche Bauteile zukünftig nicht mehr durch Originalteile ersetzt werden können.
Für den Einsatz additiver Fertigungsprozesse in der Ersatzteilfertigung sind jedoch zahlreiche technologische Fragestellungen zu klären, die im Rahmen der F&E-Arbeiten des vorliegenden Projekts im Verbund gelöst werden sollen. Die zur Erschließung und regionalen Implementierung des Business-Cases „Additive Ersatzteilfertigung“ notwendigen Forschungsarbeiten können nur im Verbund von Endanwendern, die mögliche Ersatzteile aus ihren Branchen beistellen, Fertigungsunternehmen, Softwareunternehmen und Forschungsstellen durchgeführt werden. Hierbei werden folgende Ziele verfolgt:
– Ausbau und Festigung des regionalen Innovationsnetzwerks aus vorhandenen und angesiedelten Unternehmen unter Nutzung der Potenziale der additiven Fertigung für die Ersatzteilherstellung
– Verkürzung der Einführungszeiten von AM im Bereich der Ersatzteilherstellung in verschiedenen Branchen unter Einhaltung der gesetzlichen und wirtschaftlichen Vorgaben
– Kompetenzaufbau/Softwareentwicklung zur Abbildung von Prozess-Eigenschafts-Beziehungen für die Verkürzung der Vorlaufzeit
RepAlreality
Koordinatoren des Verbundvorhabens:
Dipl.-Ing. Carsten Wedemeyer
Dr. Christin Hoffmann
Förderkennzeichen: 03WIR2508
Laufzeit: 01.06.2021 – 31.05.2023
Technologische, wirtschaftliche und soziale Innovationen sind der Schlüssel zum erfolgreichen Strukturwandel in der Lausitz. Das Teilprojekt RepAIreality bildet die Grundlage für Innovationen im Bereich Wartung, Instandhaltung und Reparatur (WI+R). Es wird die Basis für neue Geschäftsbereiche sowie Ausgründungen bzw. Ansiedlungen im Bereich WI+R geschaffen und eine attraktivere Lebens- und Arbeitsregion Lausitz gefördert.
Die Ziele von RepAIreality sind: (1) die Entwicklung eines KI-basierten Reparatur-Assistenzsystems zur Sicherung von Wissen, das gleichzeitig die Qualifizierung von fach- und branchenfremdem Personal übernehmen kann, (2) die Etablierung eines attraktiven Arbeitgeberimages und (3) die Entwicklung des Lausitzer Mittelstandes, über die Digitalisierung seiner Prozesse und den Einsatz von AR/VR-Systemen, zu einer effizient und innovativ arbeitenden Schnittstelle zwischen Gesellschaft und Industrie. RepAIreality zielt damit auf technische, insbesondere KI-basierte, aber vor allem auch wirtschaftliche und soziale Innovationen ab.
Digitale Plattform
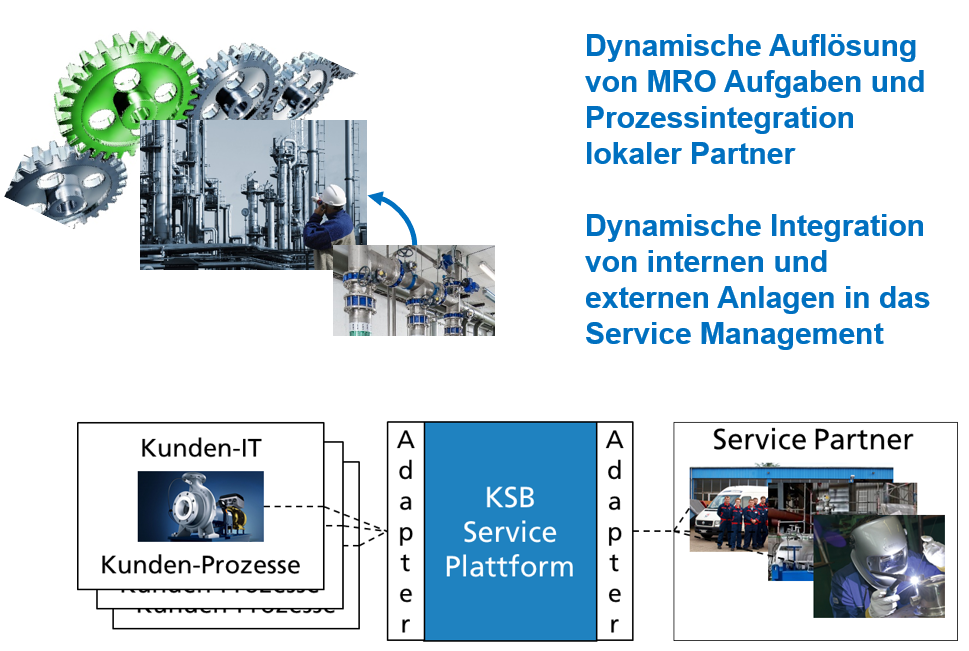
Koordinator des Verbundvorhabens:
Prof. Dr. –Ing. Thomas Knothe
Förderkennzeichen: 03WIR2509
Laufzeit: 01.02.2021 – 30.01.2024
Die Plattform – Digital Integrierte Fabrik für den Reparaturbetrieb verfolgt die Vision, dass die heute fragmentierten Fähigkeiten der Region für Wartung, Reparatur und Überholung anlass-, technologie-, objekt- und branchenbezogen in so kurzer Zeit für Assets und Prozesse zusammengestellt und konfiguriert sind, als ob sie nur für den einen Zweck entwickelt und betrieben werden. Das Ziel dieses Vorhabens ist die prototypische Entwicklung einer digitalen Plattform, mit der industrielle Serviceaufgaben in kleinere Bestandteile aufgelöst, auf Partner verteilt und deren Abwicklung überwacht werden können. Damit können die vorhandenen Kompetenzen und Unternehmen in der Region besser vernetzt und damit stabilisiert werden. Weiterhin werden damit die Fähigkeiten zur Wertschöpfung der Region erweitert. Die wissenschaftliche Zielsetzung des Fraunhofer IPK besteht in der Realisierung eines vernetzten digitalen Prozess- und Technologiezwillings, auf dem die Plattformfunktionen mit einer gemeinsamen Schnittstelle zugreifen können. Damit werden eine Komplexitätsreduktion sowie die Konfigurierbarkeit und damit die Skalierbarkeit der Plattformfunktionen ermöglicht. Für den assoziierten Partner KSB besteht das Hauptziel in der technischen Machbarkeit der Aufteilung von komplexen Industrieservices in kleinere Einheiten.